공정 단순화로 핵심부품 양산 가능성도 열어
환경공학 분야 국제학술지 ‘Applied Catalysis B-Environmental’ 게재
한양대학교 이성철 화학공학과 교수와 한국에너지기술연구원 연료전지실증연구센터 정치영 박사 연구진이 공동으로 연료전지 백금 사용량을 저감할 수 있는 MEA(Membrane Electrode Assembly, 막전극접합체)제조 원천 기술을 개발했다. 또한 공정의 단순화로 고부가제품인 MEA의 대면적화, 양산 가능성을 열었다.
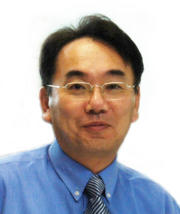
MEA는 차량용·건물용 연료전지의 핵심 부품이다. 연구진은 이번에 개발한 기술을 통해 MEA 백금 사용량을 0.1mg/cm2 수준으로 크게 줄였다. 이로써 미국 에너지성(US DOE)에서 2025년 성과 목표로 제시한 차량용 연료전지 백금 사용량 0.1mg/cm2 이하 기준을 4년이나 앞당겨 실현했다.
선진국 등 많은 나라에서 잇따른 탄소중립 선언과 함께 수소경제로의 전환기조가 이어지고, 이에 대한 대응 기술로 수소와 연료전지에 대한 관심이 증가하고 있다. 수소의 생산-저장·이송-활용단계로 구분되는 수소경제에서 활용의 핵심적 역할인 연료전지는 수송, 발전 등 다양한 용도로 확대되고 있다. 연료전지의 세계 시장 규모는 연평균 30%씩 성장해 2030년에는 약 50조원 규모로 전망된다.
고분자 연료전지는 차량용·건물용 발전을 위한 차세대 에너지 변환장치다. 고분자로 이뤄진 막을 전해질로 사용하는 연료전지로, 저온에서 반응이 일어나며 높은 에너지밀도와 효율을 보인다. 교통수단의 동력, 현지 설치형 발전 등 활용범위가 넓은 장점이 있다.
고분자 연료전지에서 전극은 슬러리 공정을 통해 백금 촉매와 나피온 이오노머가 혼재되어 있는 형태로 제작한다. 하지만 촉매 슬러리의 분산·코팅·건조 과정에서 응집 현상이 일어나 백금 촉매 표면과 나피온 이오노머의 접근성이 악화돼 산소전달 저항이 증가하고, 촉매의 활성을 떨어뜨린다.
이에 따라 가격 경쟁력을 갖추기 위해 현재 0.5mg/cm2 수준의 백금 사용량을 0.1mg/cm2 이하로 낮추면서 산소 전달 저항을 최소화할 수 있는 한층 더 높은 수준의 전극 설계 및 제조 핵심기술이 필요하다.
이를 위해 연구진은 습식 전기분무 공정을 통해 전극 표면에 이오노머를 2나노미터 수준으로 정밀제어해 얇고 균일한 나피온 이오노머를 형성하는 새로운 수직 구조의 전극을 설계했다. 수직구조의 전극은 백금 촉매, 나피온 이오노머, 공극을 수직으로 배열해 반응에 필요한 이온, 전자, 산소의 이동거리를 최적화함으로써 연료전지 성능을 극대화시켰다.
![[그림1] 습식 전기분무 공정에 기반한 신규 제조공정 순서도](https://cdn.newshyu.com/news/photo/202109/1003957_208534_1531.png)
![[그림2] 신규 제작된 전기분무 코팅 장비의 개념도 및 실제 사진](https://cdn.newshyu.com/news/photo/202109/1003957_208533_1510.png)
습식 전기분무 공정은 고전위를 슬러리에 인가해 전극 제조공정 중 전기적 척력으로 촉매와 이오노머의 고분산을 지속적으로 유지하는 것이 가능하다. 이러한 과정으로 이오노머의 박막화, 고분산화가 가능하며, 형성된 이오노머 층은 촉매의 피독률은 저감시키고 산소 이동 거리를 기존의 20~30% 수준으로 낮춰 백금 촉매의 이용률을 기존 대비 3배 이상으로 극대화시켰다.
기존의 박막전극은 이오노머 함량을 낮출 경우 전극 표면의 촉매 함량이 증가하면서 친수성이 높아져 연료전지 발전 시 생기는 물을 제거하기 어려운 단점이 있다. 전극 내 물이 너무 많으면 연료를 전달하는 통로를 막게 되면서 고전류 운전모드 시 연료부족 현상을 일으키게 된다. 또한, 전극 내 누적된 물은 연료전지 부식 반응을 활성화함으로써 촉매 지지체의 내구성에도 악영향을 준다.
이에 반해 개발된 기술은 전극 위에 코팅된 이오노머의 형상을 역마이셀 형태로 제어해 발수성을 가지는 전극을 구현하고 발전 시 발생하는 물을 쉽게 제거해 연료전지 운전 성능 및 내구성을 향상시킬 수 있다.
또한, 이 기술은 고분자 전해질막에 직접 전극을 도포하는 직막코팅 방식의 제조 공정이다. 기존 상용화된 후막코팅 방식 대비 공정이 단순하며 연속식 양산라인으로의 확장성 역시 우수해 기존 공정 대비 양산설비 설치비용은 1/2수준으로 절감되며 양산속도는 2배 이상 향상 될 수 있을 것으로 기대된다.
![[그림3] 신규 공정으로 제작된 전극층-초발수층(왼쪽), 기존 데칼전사 공정으로 제작된 전극 층(오른쪽)](https://cdn.newshyu.com/news/photo/202109/1003957_208535_1633.png)
이성철 교수는 "이번 연구를 통해 차량용·건물용 연료전지 MEA 단가를 30% 이상 저감할 수 있는 차세대 전극 제조 원천기술이 확보됐다" 라며, “기존 후막코팅 공정을 직막코팅 방식으로 전환함으로써 MEA의 양산성도 확보되어 이를 통해 정부가 추진 중인 탄소중립 실현을 위한 연료전지 보급률 달성에도 기여할 수 있을 것으로 기대한다” 라고 말했다.
연구 결과는 환경공학 분야 저명 국제학술지인 ‘어플라이드 카탈리시스 비-인바이론멘탈(Applied Catalysis B-Environmental)-IF19.503, JCR Environmental Engineering 분야 1위, 상위 0.73%) 8월 10일자 온라인 판에 게재됐다.